Roll coaters allow you to evenly apply hot melt or cold glue adhesives to a variety of substrates. Manufacturers use roll coaters for numerous materials like paper, wood, metal, and plastic.
Hot and cold roll coaters allow you to apply adhesives to flat-rolled goods using different techniques such as dipped or spray-on. You can save a lot of time and reduce costs with the right type of hot melt roll coater.
Roll coaters must be fine-tuned to meet whatever specifications the job requires. Fine tuning allows tolerances to within thousandths of an inch depending on the requirements.
How Roll Coaters Work
Essentially, a roll coater allows you to apply adhesive to the surface of your substrate quickly and evenly. Some industrial roll coaters also apply oils, paints, or other liquid coatings such as varnish.
A roll coater can be a highly specialized machine costing thousands of dollars or a simple adhesive or paint applicator.
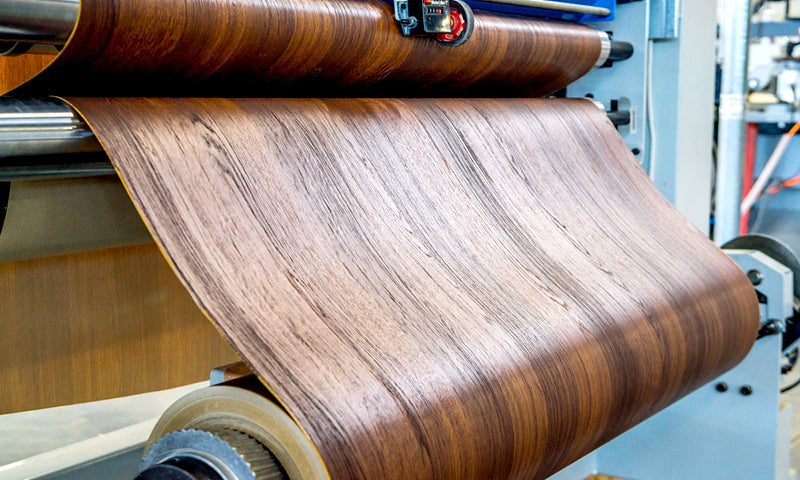
Covering for Roll Coaters
Most coating rolls always have some kind of covering that offer various resistance properties. Three of the most common types are:
#1 - Nitrile
Nitrile is a Food and Drug Administration (FDA) approved synthetic rubber coating used in the food and pharmaceutical industries. The roller core is preferably made from stainless steel to help minimize further possible contamination.
#2 - Ethylene Propylene Diene Monomer (EPDM)
EPDM synthetic rubber has excellent heat and chemical resistant properties. Manufacturers save costs by simply applying a coat, then grinding it down to the correct tolerance of the roll coating machine.
#3 - High Release Silicone
Silicone offers excellent heat resistance and provides high release. These silicone coatings are used when you use an adhesive on plastic film or paper. High release silicone costs more than other types.
The Five Most Common Types of Roll Coaters
The five most common types of coaters used for adhesives are the Gravure, Die, Reverse Roll, Flex Bar, and Rod.
Gravure
The Gravure coater has an engraved gravure roll that has a pattern that determines the exact amount of adhesive delivered. An applicator — a pressurized head or a pan, for example — applies the adhesive to the roll.
Die Coaters
A die coater pumps adhesive through a die and transfers it to the web, supported by the backup roller. The coat weight determines the speed of the pump.
Die coaters are used in label production.
Reverse Roll
Reverse Roll coaters have an applicator roll, rubber-coated backup roll, and metering roll. The substrate and adhesive are fed in opposite directions.
Flex Bar
In a Flex Bar Coater, the applicator roll picks up the adhesive coating from a pan and meters it between the flex bar gap and the applicator. Flex Bar Coaters often apply tape.
Rod
Like the Flex Bar Coater, rod coaters often apply packing tape. The rod coater has a rod, a pump, a three-part, multi-chambered pan, and an applicator roll. The coating flows into the center part of the multi-chambered pan at a constant rate. The overflow spills into the other two pans. The overflow will pick up and wash out any debris that might drop into the center pan adhesive liquid. The applicator picks up the adhesive from the center pan, transfers it to the web and continues to the rod. The rod’s size determines the film thickness before it is applied to the substrate.
Gravure, die and reverse roll work best for hot melt. All work well for solvent- or water-based adhesives.
Selecting a Roll Coater
You need to consider six factors when selecting a roll coater for your business:
#1 – Type of Adhesive
The type of adhesive used specifically affects the materials used for the rollers and the reservoirs.
Hotmelts, for example, need the machine or rollers to heat the melt before applying it to the product or material.
The materials used in the construction of the machine can affect the way the adhesives react, either degrading the adhesive to a certain extent or fouling the machinery.
#2 – The Thickness of the Substrate
To configure the feed roll correctly, you must ensure the substrate comes into full contact with the coating roller so the film of adhesive will be consistent. However, you do not want the coating to transfer to the feed rolls.
If you have flexible substrates, like thin plastic film or paper, then you want a roll coater that uses a pressure roller or a dual feed system.
Thicker substrates, such as wood, require a soft-faced roll coater system to ensure the entire surface is coated evenly.
#3 – Full Coat or Partial Coat
Depending on what part of the substrate you want coated — the entire surface, an edge, or a pattern — determine the type of roll coater machine to purchase. In addition to roll coaters that apply adhesive to the entire sheet or piece of substrate, some machines allow you to set a pattern while others only coat the edge.
#4 – Width of the Substrate
Your machine should be at least two inches wider than the surface you coat. This allows the entire surface to receive a full coat of adhesive, even when loaded crookedly.
#5 – Top or Bottom Coating and Handling
Which side of your substrate gets coated first also impacts your roll coater selection. Remember that after the material exits the machine, you must process it further, whether you are boxing, stacking, or sealing.
Coating the top portion first makes the substrate easier to handle, especially if it is going directly onto a conveyor belt to go to the next part of the process.
The least expensive machines usually coat the bottom surface, making it necessary for someone to handle the substrate immediately once it leaves the machine.
Glue contamination is always a concern, especially in sensitive environments like the food and beverage industry.
#6 – Cleanup
Use a roll coater that disassembles and cleans easily. Some need cleanup more often than others, depending on how continuously they are used.
Some of the maintenance features to look for when choosing a roll coater include easily removable tanks, separate wash tanks, removable rollers and a wash-down system for the rollers and tanks.
Datco Roll Coaters
Datco manufacturers several different quality types of roll coaters for hot melt and cold glue applications.
Hot Melt Roll Coater
The Datco Versa Hot Melt Top Coater and Roll Coater allows you to use it as either a hot melt roll coater or a top coater.
You can customize this model that is also available in knurled roll.
The Versa comes with a Teflon conveyor belt and a wide range of sizes. It can accommodate just about any type of material.
The Datco Big Roll Series Hot Melt Roll Coater comes in standard 6-inch, 12-inch and 18-inch sizes, but you can order a custom size up to 50-inch. The reservoir holds up to a pound of adhesive per roll inch. Its simple start and heat-up procedure allows you to start using it almost as soon as you turn it on.
Cold Glue Roll Coater
The Datco Cold Roll Series Cold Glue Roll Coater will apply glue from half inch up to 36 inches. It is easy to clean and does not require tools for disassembly or reassembly.
The Datco Versa Cold Series coats the top of the substrate using cold and water-based adhesives. The machine is made of stainless steel and, like the Cold Roll Series, has a reputation for quick disassembly and reassembly for cleaning.
Types of Roller Coating Defects and Remedies
Even when using a quality roll coater such as a Datco, several types of defects can occur during the roller coating process. The causes of each type vary.
Cratering
Cratering — or pitting — happens when bubbles form in the adhesive and then break, creating concave depressions in the film surface.
Oil, grease and sometimes dirt on the substrate surface cause cratering. Fisheye cratering is when silicone compounds create small craters in the substrate.
Sometimes cratering can reach all the way to the surface of the material.
Remedy: Prime the surface prior to applying the adhesive or use a higher-quality adhesive.
Crawling
Crawling happens when the liquid adhesive can’t completely cover the substrate due to low surface energy. The adhesive can fully wet the material and pull back, forming droplets and leaving some portions of the substrate without glue.
Remedy: Raise the surface energy of the substrate by removing oils and other contaminants, or use adhesives specifically manufactured to lower surface tension.
Foam
Foam may already be present in an adhesive prior to using the roll coater. It happens when air enters the adhesive. If you use gravure coating, the gravure process could also force the formation of foam.
Remedy: Prevent air from entering the adhesive and minimize the use of surfactants or substances that reduce surface tension in the adhesive.
Orange Peel
Orange peel is rough, irregular patches throughout the surface of the adhesive. Orange peel occurs when the binder doesn’t flow evenly across the substrate’s surface.
Remedy: Use an adhesive with a different viscosity.
Delamination
This happens when the surface is not clean, or the adhesive is not compatible with the substrate.
Remedy: Clean the surface of the substrate thoroughly and check the manufacturer’s guidelines to ensure compatibility between the material and the adhesive.
Roll Coater Maintenance
You can leave most hotmelts or liquids that don’t dry, like oils, on a machine. However, you must clean out most other types of glue from the machine. Liquid rollers can clog, or chemicals can coagulate and foul the interior workings.
For larger roll coaters, you can use an acid flush procedure to thoroughly clean all parts.